Products via anisotropic etching of silicon. Comparisons of simulated results to SEMs of etched structures show very good accuracy. Etch depths and feature sizes are captured accurately by the simulation. The number of microfabrication test iterations needed for bulk silicon etching has been reduced in facilities that utilize this etch. Anisotropic crystalline etching simulation (ACES) program based on a new continuous Cellular Automata (CA) model, which provides improved spatial resolutionand accuracy com-pared with the conventional and the stochastic CA methods. Implementation of a dynamic CA technique provides in-creased simulation speed and reduced memory requirement (5x).
Bill Foote
EECS Department
University of California, Berkeley
Technical Report No. UCB/CSD-90-595
September 1990
http://www2.eecs.berkeley.edu/Pubs/TechRpts/1990/CSD-90-595.pdf
Model has been successfully developed to a 3-D silicon anisotropic etching simulator (SEAES). The etching conditions, such as etchant temperature, etchant concentration and doping concentration, which effect the etch rate of different crystal planes, can be conveniently inputted by using the Graphical User Interface (GUI) of SEAES. Anisotropic Crystalline Silicon Etch Simulator (ACSES) Posted by MA-tek Taiwan ⋅ July 17, 2012 ⋅ Leave a comment Design different BMP or CIF or GDS files, and run Silicon Etching Simulations on ACSES.
A series of programs have been developed to model anisotropic etching of crystalline substances. The focus of this work was on the computation of the geometric offset surfaces for a given object, when the etching of different faces progresses at different rates depending of face orientation. Programs have been developed to calculate the emerging shapes for both two- and three-dimensional geometries.
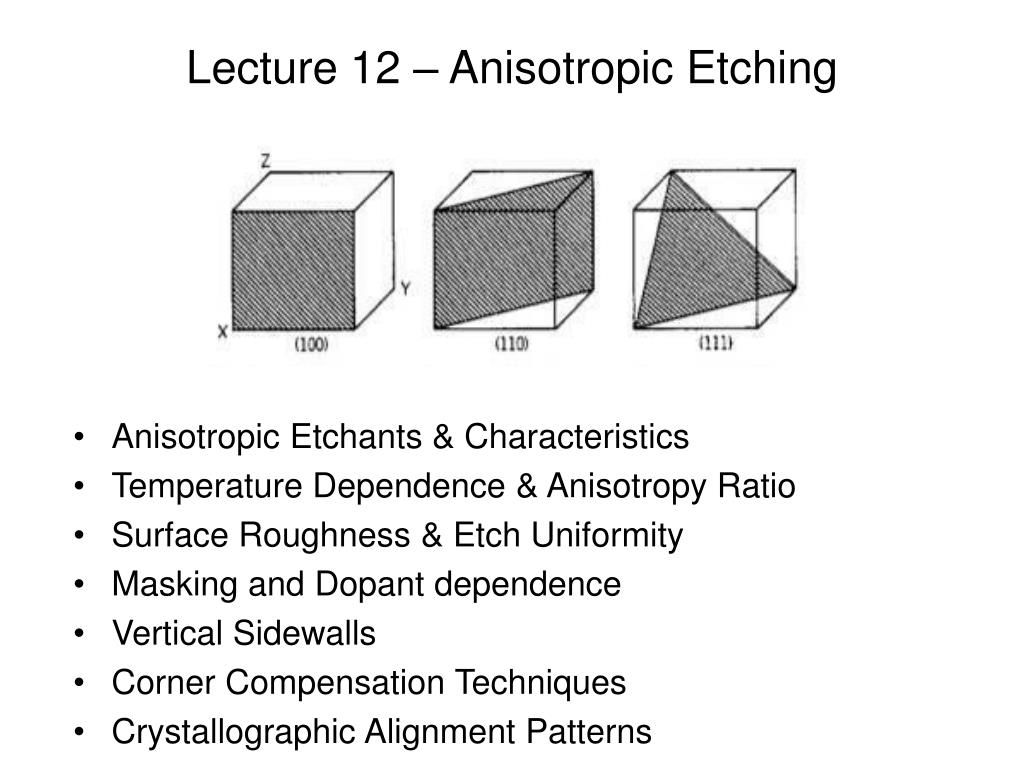
Since complete information about the anisotropic etch rates in all possible directions have been published for only very few combinations of crystals and etch solutions, we also had to write a rudimentary generator that would produce plausible and self-consistent direction-dependent etch rate functions. This modeling proceeds in stages: From the geometry of the crystal lattice, its atom spacings and angles between bonds, some inferences are made about the probability that certain more or less exposed atoms get attacked and removed by the etchant. With this model the etch rates for several key directions, i.e., for the simple crystallographic planes (100), (110), (210), (111), (211), and (221), have been calculated. The etch rates for the direction in between these key orientations are found by interpolation.
The etching simulator then uses such an artificially generated function or any function that may come from experimental observations and applies it to arbitrary polyhedral shapes. For all edges and vertices it first determines what new bevel faces might form because of strong local maxima and minima in the etch rate function. Then all the faces, the original ones as well as the bevel faces, are advanced at their corresponding etch rates and combined into a new consistent surface description of a solid object. The user can specify the total etching time and the number of intermediate states that should be displayed. The shapes obtained from the etching simulator programs are in good qualitative agreement with the kinds of shapes actually observed in the laboratory.
BibTeX citation:
Anisotropic Crystalline Etch Simulation Tools
EndNote citation: